では実際の張り合わせですが、現在のリカーブ用リムの幅は一番広い部分で40〜50ミリ弱で作られています。これらの幅の成形は接着後に行われます。最初の接着段階では60ミリ程度の均一幅の芯材とFRPなどを張り合わせます。ちょうど最初はスキー板のような(先端は丸くなっていませんが)ものが作られると考えると分かり易いでしょう。 |
接着剤を均一に塗布した複数の素材を重ね合わせて、もうひとつの基本性能を決定付けるリムの形状をした「木型」に挟みこみ、高圧・高温をかけて接着剤の完全硬化を待ちます。サンドイッチ製法と呼ばれるのはこのようにしてリムの原型が作られるからです。しかしスキー板やテニスラケットあるいはゴルフクラブであれば、このように成形された形がほぼそのまま製品として使われるのですが、アーチェリーのリムはそうではありません。この原型にストリングを張り、それだけではなく実際の使用では20数インチ引かれては放されという、他には例を見ない過酷な条件下で性能と耐久を試されます。 |
ところでリムの強さはどこで決まると思いますか? 同じモデルのリムであれば35ポンドのリムも40ポンドのリムも、素材構成や形状そして幅は同じです。では、どこで強さの違いがでるのか。 |
リムの表面を削ってポンドを変えると思っているアーチャーも多いでしょう。たしかに塗装前には仕上げとして表面を削る(磨く)ことはしますが、ポンド変更をするくらいに削ることはFRPの表面の繊維自体を切ることであり、性能や耐久に大きな問題を及ぼすために行うことは適切ではありません(しかし普及モデルなどではないとは言い切れません)。ではどこで変えるかというと、実は芯材なのです。すべてのメーカー、すべてのモデルがそうとは言いませんが、多くの場合この方法がとられます。最初に芯材にテーパーが掛かっていると言いましたが、この長さ方向に対するほんの少しの厚みの違いのどの部分を使うかで調整したり、芯材そのものの厚さの違うものを何種類も準備している場合もあります。ともかくは芯の厚さでポンド(出来あがりの強さ)を変えていきます。しかし40ポンドのリムを作ろうと思って、ピッタリその強さが出来あがるかというと、このあたりはメーカーのノウハウと職人技がものを言うところです。実際の生産では例えば40ポンドのリム1ペアだけを作ろうとするのではなく、作る時にはそのあたりのポンドを狙って数ペアから、場合によっては数10ペアのリムが生産ラインに同時に流されることになります。 |
余談ですが、メーカーにもよるでしょうがリムを作る時は当然その生産性(歩留まり)や素材の準備などから考えても、いろいろな強さや長さのリムを一度に並行して作るということはしません。例えば66インチ用40ポンドのリムと64インチ用30ポンドのリムを同時に生産ラインに流すことは、後で話をする「ペア組み」段階においても非常に効率が悪いことになります。そのため普通は66インチの40ポンドを狙って何ペアものリムが一度に生産され、結果的にはその前後の66インチ39ポンドも41ポンドも、そして当然40ポンドも出来あがるというわけです。このように、リムはいくつもの工程をグループに分けて進んで行きます。そのため通常、最初の仕込みから完成までには数週間が必要となります。 |
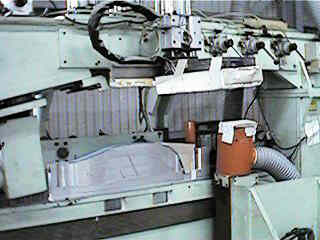 |